品質
TEL Quality Global No.1
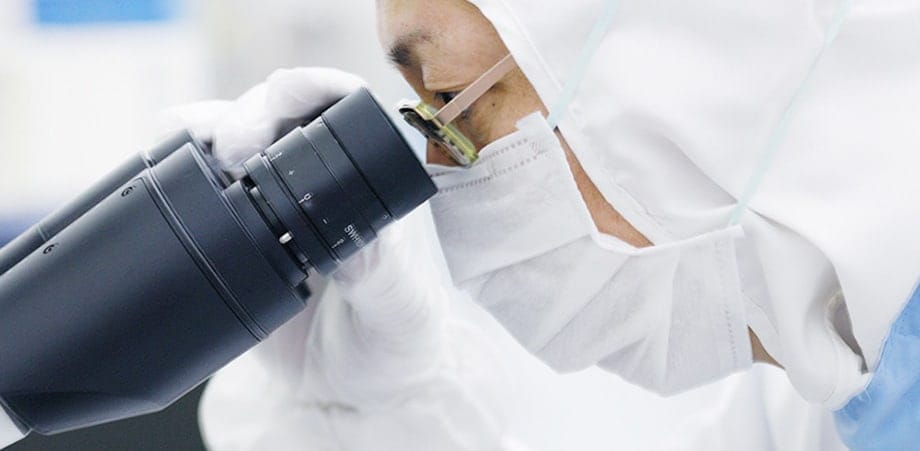
お客さまの真のニーズを理解し、世界No.1の品質を追求します。
品質についての考え方
東京エレクトロンでは、品質についての考え方として、「東京エレクトロングループは、提供する製品およびサービスが高い品質であることを目指します。それは開発に始まり製造・据付・保守すべての工程を含む、また営業活動の顧客対応業務も品質とみなします。わたしたちは、お客さまの成功を支える高品質の製品とサービスおよび革新的なソリューションを提供し続けます」と定義し、品質方針を次のように定め、その実践に努めています。
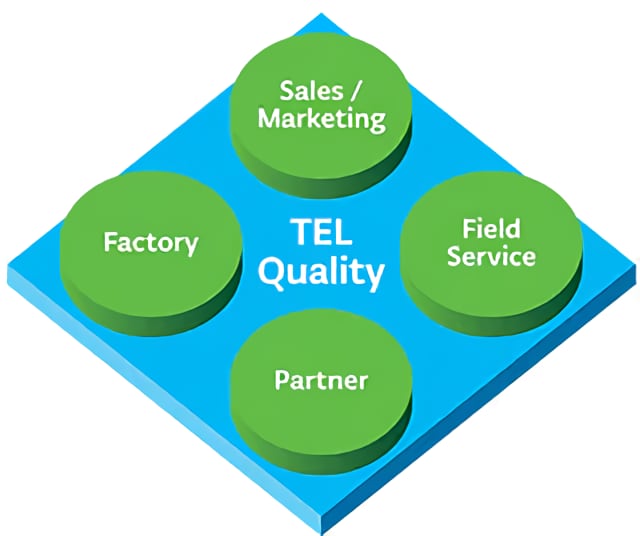
- 「品質優先」
- 品質の安定は顧客満足のみならず、期待通りの生産計画を達成し、メンテナンス負荷を低減する基盤であり、一時的なコスト増よりも優先します。
- フロントローディングと自工程保証
- 最先端の技術に基づき開発設計段階から品質をつくり込み、すべての業務プロセスにおいて、自らの工程品質を完結することで、高品質の製品を提供し続けます。
- 品質と信頼
- 品質に問題が生じた場合には、製造・販売・サービス部門が一丸となって、事実に基づき本質的な原因究明に全力で取り組み、速やかな解決に努めます。
- 継続的改善活動
- お客さまの満足・信頼につながる活動に対して、品質目標や指標を設定し、PDCAサイクルを回しながら、継続的改善を実施していきます。
- ステークホルダーとのコミュニケーション
- 製品品質に関わる必要な情報をタイムリーに発信するとともに、ステークホルダーの期待に適切に対応していきます。
この品質方針は当社グループ全社統一の方針です。 中期経営計画のGT2025達成に向けた3つの強化項目である“製品競争力強化”“顧客対応力強化”“利益体質強化”にも繫がっており、各人の行動にも深く関わることから、工場のみならず本社やグループ海外拠点にも適用するものです。品質方針ポスターを製作し、言語は、日本語版のほか、英語版、中国語版(簡体字)、韓国語版を作成し、各国の各社・全拠点へ配付し掲示しております。
当社は、高品質な製品を安定して提供するため、CEOを責任者とした品質保証体制を構築し、運用しています。当社グループ内のすべての製造会社が、品質マネジメントシステムの最新規格であるISO 9001の認証を取得している他、各製造会社において定期的な内部監査や第三者機関による中立かつ公正な監査を実施し、品質マネジメントシステムの維持や改善につなげています。
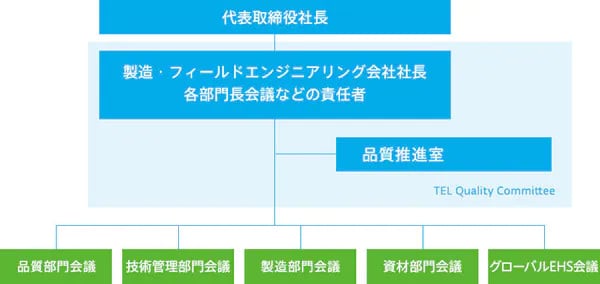
ISO 9001認証取得状況
会社名 | 事業所名 | 認証番号 | 取得年月 |
---|---|---|---|
東京エレクトロン テクノロジーソリューションズ | 藤井事業所/穂坂事業所 | 00225-1994-AQ-KOB-RvA | 1994年9月 |
東北事業所 | 1994年12月 | ||
東京エレクトロン九州 | 合志事業所 | 5569-1997-AQ-KOB-RVA | 1997年3月 |
TEL Magnetic Solutions | ー | IE09/66498 | 2009年11月 |
東京エレクトロン宮城 | 大和事業所 | 02609-2012-AQ-KOB-RvA | 2012年9月 |
Tokyo Electron Korea | Balan Plant | QSC1680 | 2011年9月 |
TEL Manufacturing and Engineering of America | Chaska Office | FM586277 | 2013年3月 |
Tokyo Electron (Kunshan) | ー | 260147-2018-AQ-RGC-RvA | 2018年5月 |
工程改善活動
お客さまの製造現場では、装置間における品質のばらつきの抑制、正確なプロセスの再現性、高い生産性が求められています。こうしたお客さまのニーズに合致する製品を提供するため、当社が注力するのが統計的手法を使った工程改善活動 (PCS*)です。
各種重要部品 (ウェーハに直接接触する部品や、機械的、熱的、電気的または電磁気的エネルギーをウェーハに伝達する部品など、装置のプロセスに直接的な影響を与える部品) の情報を管理図化してばらつきの分析をおこない、製造工程の変化を速やかに検知し、対応します。こうしたPCS活動を、特定の重要部品を扱うお取引先さまとともに取り組むことで、部品品質のばらつきの抑制や良品製作工程の維持・改善に努め、お客さまの期待を上回る製品の提供へとつなげています。
また、新たな重要部品を扱う製作工程は、常に見直しや改善を必要としますが、当社の装置は数万にも上る数の部品で構成されており、その中から特定の部品を選択して定期的に集計・分析をおこなう作業には、多くの工数を必要とします。
この作業の適正化と効率化を図るため、当社はお客さまからの情報収集、国内製造拠点間での協議、お取引先さまからのヒアリングなどを実施し、自動化も含めた業務フローの見直しやシステムの改善などを進めています。Shift Leftの考えに基づくこれらの活動を継続的に実施することにより、さらなる生産性の向上に取り組んでいます。
PCS: Process Control System
取り組み事例
東京エレクトロン テクノロジーソリューションズ (東北) では、統計学に基づく実験計画法*を用いた重要部品の品質指標を設定し、お取引先さまとともに品質活動のレベルアップを進めています。
実験計画法で設定した最良な品質指標を目標として定め、重要部品の製作工程における検査値や調整値などのばらつきが生じる条件をPCS活動で厳密に管理し、製作工程の正確性と安定化を図っています。
今後はお取引先さまの品質に関するデータ取得から判定までの処理について自動化を促進し、リアルタイムに品質の状態を検知することで、重要部品の製作工程のさらなる改善に取り組んでいきます。
実験計画法: 効率の良い実験方法を設計し、結果を適切に解析することを目的とする統計学の応用分野
自工程保証の徹底とShift Left の推進
製品の品質向上のためには、上流工程で不適合を生じさせないようにするとともに、各工程における品質管理を徹底し、不適合が生じた場合においても不適合品を後工程に流さないようにすることが重要です。この観点から、当社では自工程保証に重点を置いた活動を推進しています。特に、製品設計の初期段階からのリスク抽出と対策 (FMEA*¹)を確実に実施し、各工程における徹底した審査や、シミュレーションを使用した検証などを実施することで、さらなる品質の向上を目指しています。
この自工程保証活動を通じて、各工程の精度向上や手戻りによる対応コスト*²の低減に取り組むことで、上流工程における付加価値の高い技術および製品の創出を可能にするとともに、Shift Left*³の推進にもつなげています。
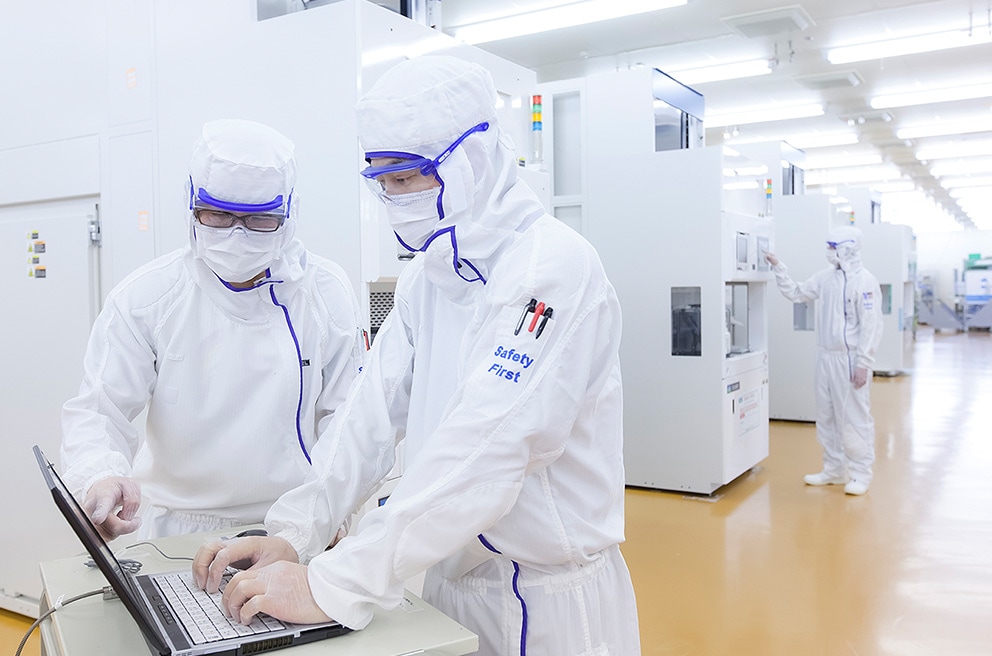
さらに当社は、Product Lifecycle Management (PLM) を推進し、自工程保証で徹底管理された製品企画から開発、設計、製造、サービスまでの全工程を包括的に管理し分析することで、製品の早期リリースや業務の効率化、品質の向上やコストの削減に努めています。
FMEA: 品質についての考え方参照
手戻りによる対応コスト: 不適合が生じた際に工程をさかのぼってやり直すためのコスト
Shift Left: 参照
Shift Left(フロントローディング)の取り組み
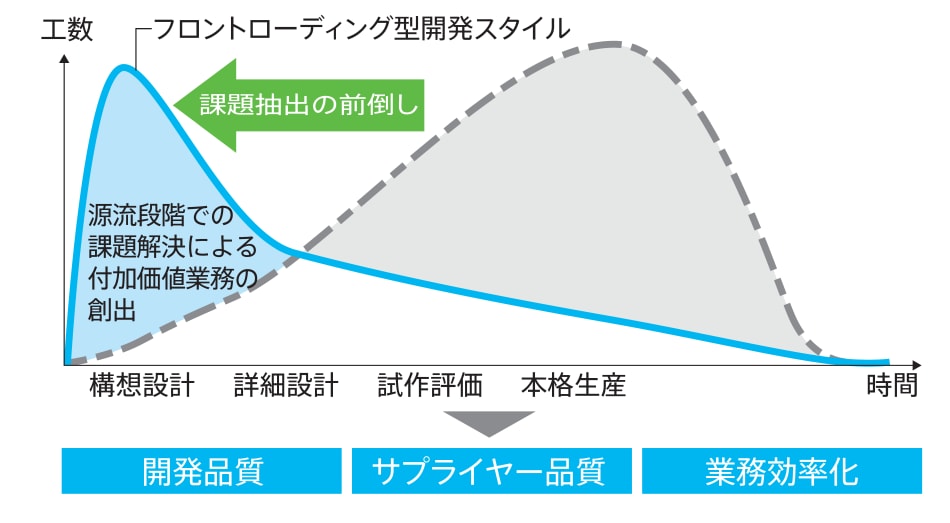
再発防止・未然予防のための対応
当社は、各製品に適した独自の設計ルールを定め、ISOやEN*¹といった安全規格への適合を進め、より高いレベルの安全性を追求しています。同時に、安全に配慮した製品づくりのための体制、および装置の設計・製造上の不適合や、作業中に発生した事故などに対応するための体制を整えています。
事故発生時は、事故報告システム「TIRS*²」によって、各事業部の安全・品質の関係者や責任者、トップマネジメントを含めた経営層に情報が配信され、直ちに事故調査をおこなった上で原因の特定と再発防止策を立案します。
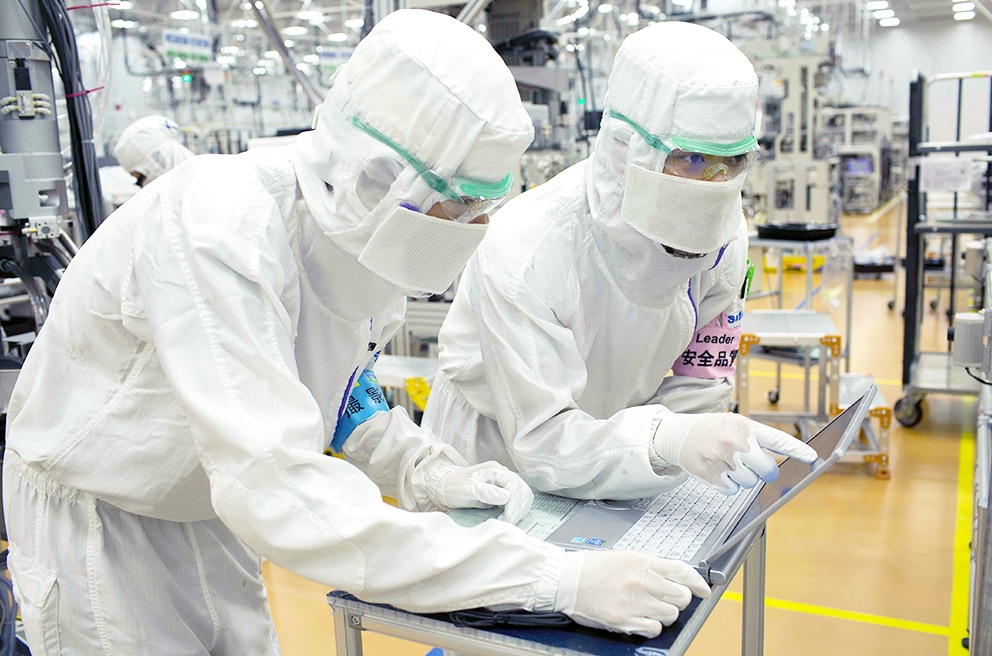
装置の重要不適合や品質の情報については、当社の運用規程に準じて当社独自のシステムである「QA-BOX*³」を運用し、品質部門全体で共有します。事故調査の結果から得られた対策については、問題が発生した装置のみならず他のお客さまの装置にも速やかに反映するとともに、究明した根本原因から現行の設計基準やプロセスフローを見直すことで重要不適合の恒久的な再発防止に努めています。
事故調査の対象となった部門では、品質部門長とともにQA-BOX定例会にて他の装置への波及性や共通性を検証し、課題とその対策を共有することで、類似不適合の未然予防に向けたさまざまなアプローチを検討しています。またQA-BOX定例会で決定された共通方針を速やかに当社のグループ全体へ展開し、対象となる装置に反映することで、装置に起因する不適合事例の低減につなげています。
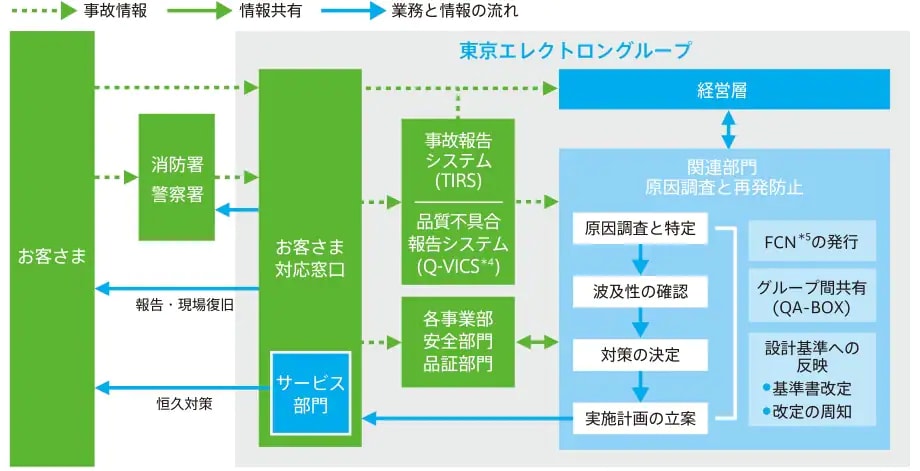
EN: European Norm。EC指令 ( ニューアプローチ指令) には明記されていない技術基準の部分を補完すべく制定されたEUの統一規格
TIRS: TEL Incident Report System
QA-BOX: 当社内の重要品質情報の共有・横展開ツール
Q-VICS: Quality Valuable Information Chain System
FCN: Field Change Notice。一般的なリコールを指す
お取引先さまとの取り組み
品質の高い製品を迅速に市場へ提供するためには、お取引先さまとの強いパートナーシップに基づく継続的な品質の向上が欠かせません。当社では、2000年度より独自のアセスメントシステム「Supplier Total Quality Assessment(STQA)」を実施し、当社が目指す品質についてお取引先さまに十分にご理解いただけるよう努めています。
当社は、お取引先さまと新規の取引を開始する際においてもSTQA を使用し、製品品質やコスト、情報セキュリティ体制、企業の社会的責任分野における人権、倫理、安全、環境などの取り組みについて、セルフアセスメント形式でチェックをおこないます。このチェックにおいてリスクが確認された場合には、お取引先さまを訪問し、現場で不適合箇所を確認しています。お取引先さまには、当社の品質や関連する重要事項についての考え方を共有させていただいた上で、改善策の立案と実行をお願いするとともに、それらすべてが完了するまで継続的なサポートを提供しています。なお、重要部品を扱うお取引先さまや品質に関する問題が確認されたお取引先さまにおいては、3 年ごとに監査を実施しています。
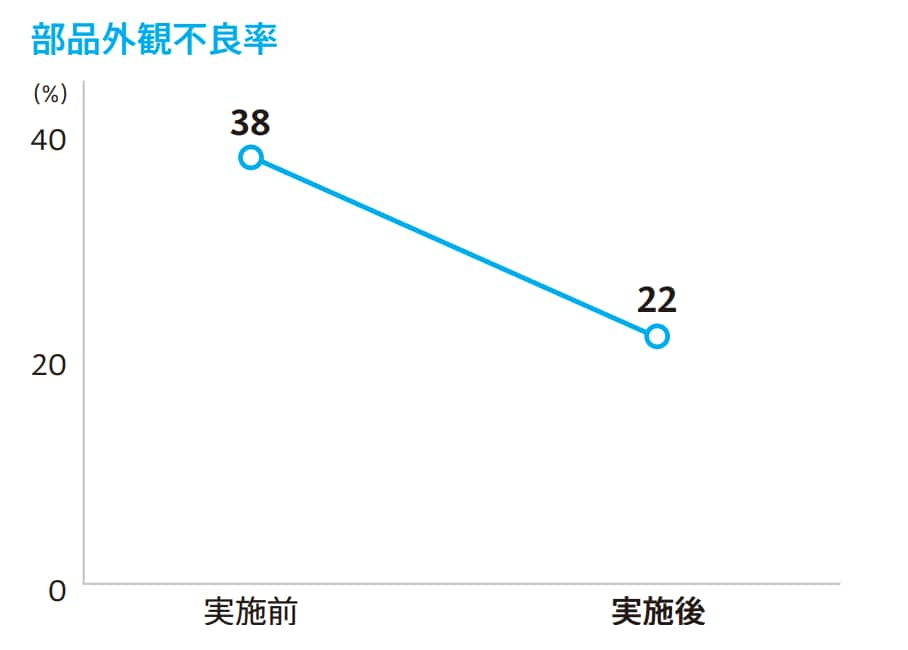
また、STQA を運用する国内各製造拠点のリーダーと定期的に会議を開催し、お取引先さまに関する情報の共有や課題の解決に向けた検討をおこなっています。
取り組み事例
東京エレクトロン テクノロジーソリューションズ品質保証部門では、部品不適合の兆候を早期に発見できるよう、受け入れ検査工程の強化に取り組んでいます。受け入れ検査時に発見される不適合は、傷や打痕による部品外観の不良が全体の約4割を占めています。お取引先さまとともに原因の究明をおこない、適切な包装材を選定するなど、部品外観の改善と強化に取り組んだ結果、2021年度は出荷台数が増加したにもかかわらず、目標値130ppm(100万件当たりの不適合品130件)を達成しました。今後も、お取引先さまとの連携を強化し、継続的な改善活動に取り組んでいきます。
品質教育
当社では、さまざまな教育プログラムを実施することにより、従業員一人ひとりの品質に対する意識の向上に努めています。
新入社員を対象とした基礎的な品質教育や、TELグループ全従業員に対する「PDCA教育」などのプログラムをグローバルに展開しています。「PDCA教育」においてはPlan(計画)、Do(実行)、Check(評価)、Act(改善)の4つのプロセスによる継続的な改善の必要性を学びます。2019年度では本プログラムの受講率は84%となりました。
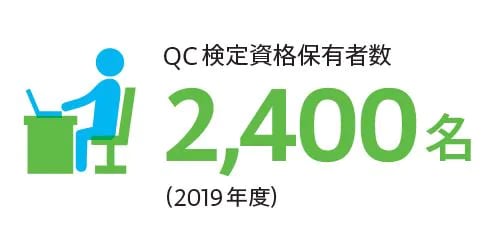
また、重要問題の解決手法を習得する、独自の教育プログラム「TEL 6-Step」を品質管理と密接に関わる開発者、設計者、品質管理担当者、サービス担当者を対象に実施しています。このプログラムは、品質管理における一般的なトラブル分析手法である「8D問題解決手法*¹」をTELの問題解決プロセスに置き換え、変更しています。問題の本質を徹底的に掘り下げ、技術的要因や根本原因を究明することにより、問題を早期に解決し、また再発防止策を講じる能力を養成します。2019年度で、本プログラムの受講者数は5,800名となりました。また品質管理リーダーを対象とする集合研修を開催し、演習形式で品質問題の解決について学ぶ機会を提供し、開発・製造現場における業務改善能力のさらなる強化を図っています。なお、従業員が自発的に品質改善に取り組めるよう「QC検定*²」(品質管理検定)を広め、基本的なスキルの習得を推奨しています。QC検定の資格保有者は2011年度から年々増加し、2019年度では約2,400名となりました。
8D 問題解決手法: 品質改善のための問題解決を8つのプロセスでおこなう手法
QC検定: 一般財団法人日本規格協会・一般財団法人日本科学技術連盟が主催する品質管理検定。資格保有者数は全国で累計46万名を超えている(2018年2月現在)